When reindustrialization and coopetition go hand in hand in the world of sports shoes
850 million euros: that's the sum the French government has decided to commit to encourage industrial relocation in France.
Frédéric Le Roy, University of Montpellier and Camille Bildstein, University of Montpellier
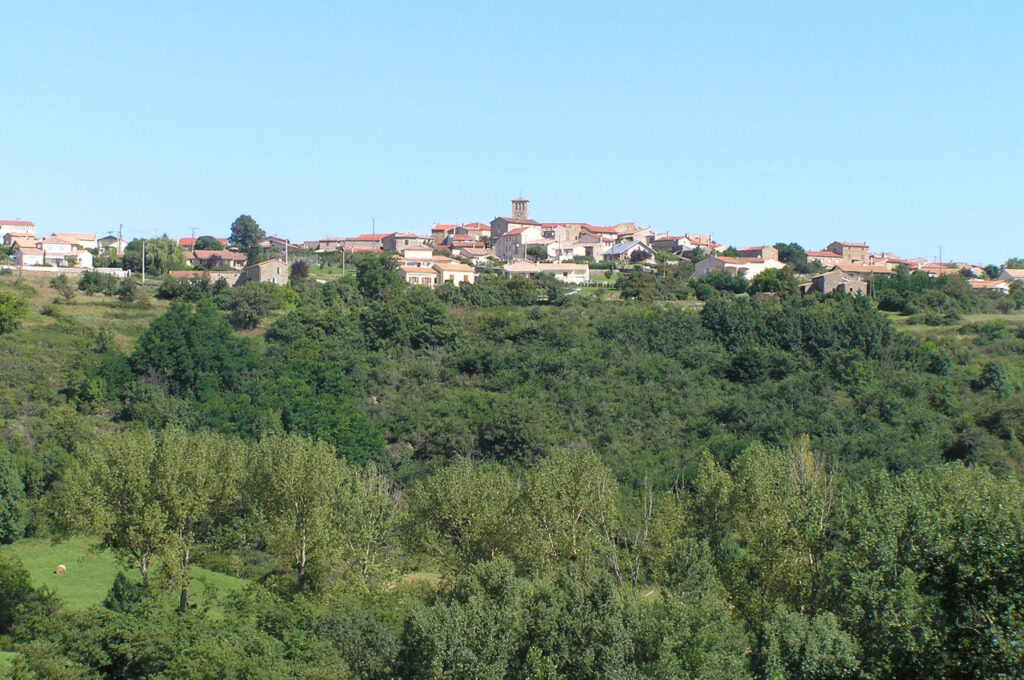
A priority born of the Covid crisis and the logistical difficulties it created, it was reaffirmed by the French President at the Paris Motor Show. The funds were used following calls for projects in five sectors considered "critical": healthcare, agrifood, electronics, essential industrial inputs (chemicals, materials, raw materials) and 5G. A total of 477 projects were selected.
For many, however, like the economists Elie Cohen and Pierre-André Buigues, who recently wrote an acerbic column in Le Monde, we're a long way from the mark. One of the main obstacles remains production costs, which are still very high in France compared with emerging countries, and inflation and fears of energy shortages are not helping.
Cooperation between competitors
In addition to government subsidies, our research work at the Coopetition Lab and the Coo-innov Chair indicates that one strategy seems to be quite effective, and should certainly be promoted: cooperation between competitors, sometimes referred to as "coopetition". Not only does it reduce costs by pooling them, since competitors often produce from similar infrastructures, but also, by sharing knowledge, it enables ambitious programs to be launched and encouragesinnovation. On this last point, let's recall how BioNtech and Pfizer researchers quickly got together and pooled their knowledge to create the first effective vaccine against Covid.
Co-operation is a strategy whose value for companies is increasingly recognized. It is just as relevant for projects carried out by large companies in high-tech sectors, such as the Galileo project, or video game development at Ubisoft, as it is for small companies in traditional sectors such as wine.
[Nearly 80,000 readers trust The Conversation newsletter to better understand the world's major issues. Subscribe today]
Salomon, Babolat and Millet, three big names in the sports footwear sector, are a prime example of the success of this strategy, based on a project to reindustrialize France. All three, with the aim of relocating their production to France, agreed to have part of their footwear produced by the same subcontractor, Chamatex, in the same factory, which they financed together somewhere in the north of the Ardèche region, in a small village of less than 2,000 inhabitants.
Competing with Asia
In 2020, Chamatex, a manufacturer of chemical textiles, launched the Advanced Shoe Factory 4.0 project (more quickly referred to as "ASF 4.0"). After a year's work and 10 million euros of investment, the sports shoe factory was inaugurated. Its purpose? To put France back at the heart of footwear production and compete with Asia. Part of the plant's investment costs were jointly borne by three customer companies, originally three competitors: Salomon, Babolat and Millet. Each contributed 400,000 euros.
The plant's high degree of automation is designed to create a flexible production line capable of manufacturing several types of footwear for the three competing brands. Footwear from Babolat, Millet and Salomon to be produced by the ASF 4.0 will essentially be made from a common technical fabric, Matryx. Matryx was originally invented by Chamatex and Babolat, and is used in new, lighter, more resistant shoes with optimum support. Millet and Salomon will therefore benefit from technology developed by a competitor.
Just a gift from Babolat? Without the cooperation with competitors, the factory would not have been possible, since its profitability is based on large-scale production, which allows economies of scale and amortization of investments.
The modernity of the plant also means shorter production times. As they conquer the European market, the three competing partners will also be able to demonstrate their responsiveness. Finally, production as close as possible to consumers minimizes transport costs throughout the supply chain, as well as environmental costs linked to the carbon footprint.
Counter-intuitive but inspiring
Ultimately, the factory should enable the relocation of almost 50 jobs in France. The idea behind this project is to replicate this factory model, and above all this cooperative model, in other geographical areas, in order to continue to relocate shoe production in France.
Co-operation may seem counter-intuitive: a priori, companies prefer to develop their projects alone. And if they don't have the necessary skills or resources in-house, they will seek partnerships with non-competitors. Teaming up with competitors is often a last resort.
The fact remains that this exemplary case shows unambiguously that coopetition, by enabling lower costs, flexibility and the sharing of innovations, proves to be a relevant strategy for the relocation of industrial activities in France. The French government could therefore have been more attentive to the fact that, in responses to calls for projects for relocation, competing companies submit a response together rather than separately.
Encouraging this type of strategy, as is the case with competitiveness clusters, could be an alternative method to the current call for projects. Beyond government incentives, the Chamatex project could be a powerful source of inspiration for all French manufacturers.
Frédéric Le Roy, Professor of Strategic Management - University of Montpellier and Montpellier Business School, University of Montpellier and Camille Bildstein, Research Engineer, University of Montpellier
This article is republished from The Conversation under a Creative Commons license. Read theoriginal article.